
BRAKES
Braking systems are designed to reduce a vehicle’s speed and bring it to a halt within certain thresholds in terms of space and time, generally by using the brakes to subject the transmission, semi-axes or, more frequently, the wheels, to resistant torque capable of absorbing the vehicle’s kinetic energy.
Most passenger cars on the road today are fitted with hydraulic brake systems, made up of brake master, brake cylinders and braking correctors.
In its simplest form, a hydraulic braking system is comprised of:
- a brake engagement device, generally a pedal;
- a piston pump (master cylinder) driven by the engagement device, fed from a reservoir of brake fluid, and linked to the braking assemblies through a network of rigid pipes and flexible hoses.
This basic circuit has evolved over the years and now also includes:
- a vacuum servo that boosts the braking effort applied by the driver;
- a divided-line brake circuit that engages the front and rear brake assemblies separately and independently from each other.
Braking systems were further developed with the introduction of braking regulators designed to check the skidding of individual wheels and ensure ideal braking conditions at the very limits of road-surface adherence.
Braking technology entered the electronic age with integration of increasingly advanced automatic braking systems such as ABS and ESP.
BRAKE MASTER CYLINDERS
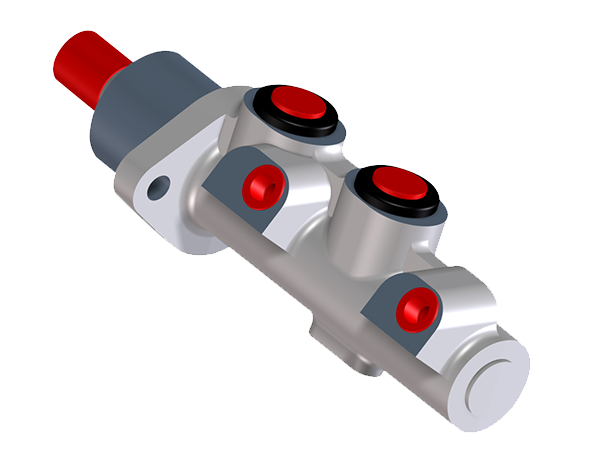
WHEEL CYLINDERS
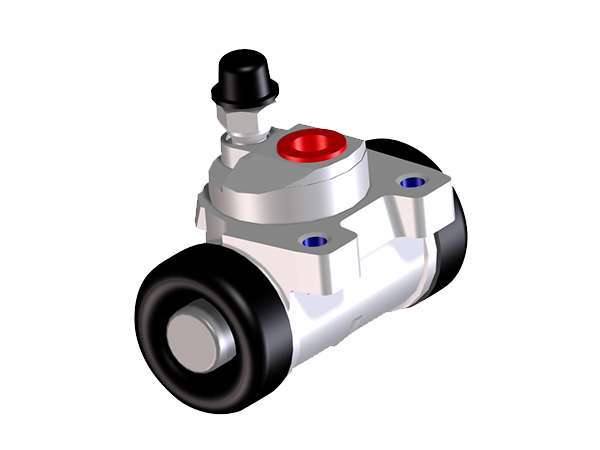
The hydraulic pressure built up in the brake pump is transmitted to the brake calipers through the pistons of the slave cylinders. The hydraulic seal of the circuit is ensured through washers installed on the body of each piston. When the brake is not engaged, each piston remains in constant contact with the related brake caliper, thanks to a spring.
Pistons are normally used in hydraulic drum brakes:
- With floating caliper: hydraulic pressure forces the two pistons of the brake cylinder to push the shoes against the internal part of the drum. Two cams are used to periodically adjust the clearance between the shoe and the drum;
- With floating caliper and floating cylinder: this self-adjusting hydraulic braking systems maintains the length of the pedal run constant, regardless of the wear and tear on washers. Self-adjustment takes place during service braking, rather than when the handbrake or parking brake is applied.
PRESSURE SELF REGULATING VALVES
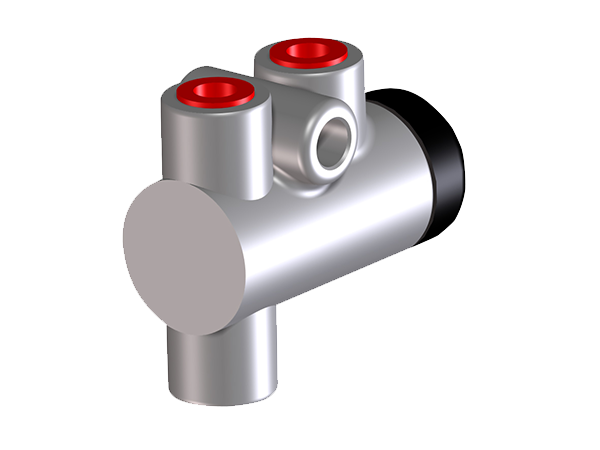
For optimal braking, the wheels must never be completely blocked. During braking, load is transferred to the rear axis of the vehicle, reducing stress on the front axis. Since the maximum braking force an axis can withstand is directly linked to its weight and the adherence coefficient, it is clear that the braking effort applied to the front and rear axles, must not be equal. Given that it is difficult, for mechanical reasons, to adjust hydraulic pressure in a rear circuit in the presence of dynamic loads, a compromise must be reached. The two types of modern braking correction systems – load reducers and compensators – provide results that are sufficiently close to optimal braking conditions.
CLUTCHES
When they first appeared on the French SIMCA 1000 in 1961, hydraulic clutch systems marked an important milestone for the automotive industry. The sensitivity and performance of the new system which provided almost optimal results, allowed for a smooth, gradually accelerating, and generally pleasant drive.Since the frame was hydraulically linked to the gearbox by a flexible hose under pressure, the issue of unwanted vibrations did not even arise. Moreover, hydraulic clutch systems are justified whenever the cable clutch alternative proves problematic. From a design standpoint, the clutch pump is very similar to a simple brake pump, generally without a bottom valve. The clutch cylinder resembles a blind brake cylinder (one-sided application with single piston) in the “standard” version or it includes a bearing in the “concentric” version which is fitted directly on the clutch mechanism (Concentric Slave Cylinder).
CONCENTRIC SLAVE CYLINDERS (CSC)
However, the evolution of the “clutch” complex, the introduction of dual-mass flywheel technology and the need of ever greater force implemented in compliance with driver comfort, required the evolution of the mechanical bearing in the current hydraulic bearings (Concentric Slave Cylinder or, simply, CSC).
Currently, CSC technology is used as original equipment for many vehicle models launched on the market in the recent years.
WORKSHOP
For this product, it is required proven QUALITY, since its malfunction involves, at best, its replacement and, at worst, the replacement of the whole clutch system assembly if this is contaminated by oil leakage from the bearing.
THE MARKET
Since this is a technology established in the last 10 years, the market of this component is in strong growth, together with the circulating park that fit it, and becomes an important topic for the whole supply chain.
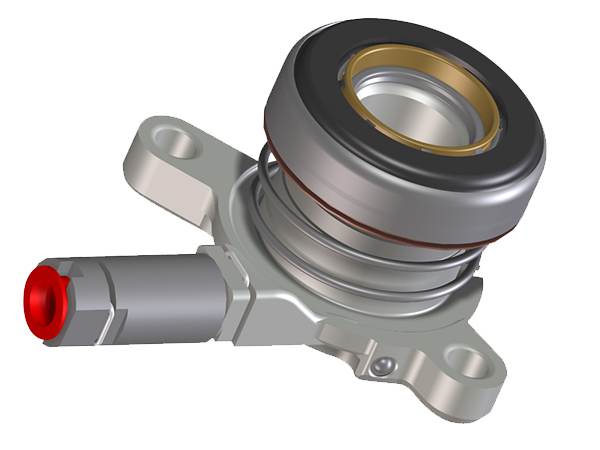
CONSTANT VELOCITY JOINTS
Constant velocity joints are typically used in vehicles with front-wheel drives. Motion is transmitted between the differential and the free and steering wheels, via two homokinetic joints linked by an intermediate shaft, with one side of each joint subjected to fixed rotation, and the other differential side, to sliding rotation, as to allow for axial movement.
This allows for maximum kinetic elasticity on each wheel, even when faced with the most demanding road conditions.
Our joints are supplied:
- pre-greased
- with plastic cap
- together with a ring clip or elastic ring (not fitted on the joint)
- with other accessories as required (e.g. dust covers)
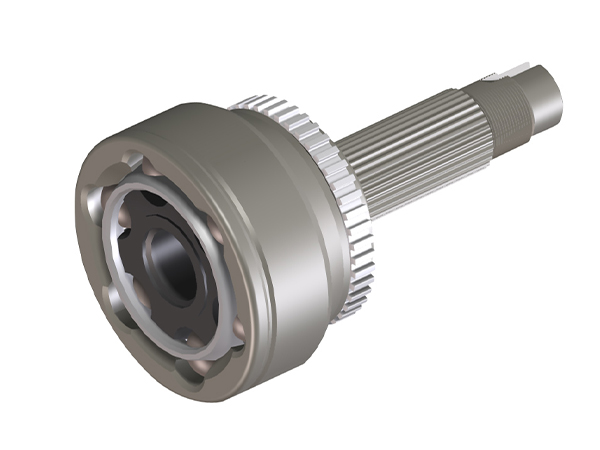
WATER PUMPS
A centrifugal pump is a device that uses the rotation of an impeller to increase the fluid pressure speeding up the flow of the fluid through the pipes. The fluid reaches the impeller near the rotation axis, it is sped up and it exits radially.
The automotive water pumps are planned specifically for their function, ie, to move the coolant through the cooling circuit.
Nuova Tecnodelta designs and manufactures the water pumps making sure that they are perfectly interchangeable with the O/E-OES respecting form, fit and function principles. The Water Pump is the main part of the cooling system of the engine. It ensures the flow of the cooling liquid through the circuit, inhibiting the overheating of the engine.
DISTRIBUTION KITS WITH WATER PUMP
The maintenance on the distribution no longer requires individual components, but complete assemblies that make easier the replacement ensuring the highest reliability.
Our range of Distribution Kits with Water Pump is the perfect solution for a constantly changing market.
We ensure perfect interchangeability with the original components combined with the highest quality: components of equivalent quality to the OE standard quality for passenger cars and light commercial vehicles.
Inside our package you will find Dayco Belts, Water Pumps of Nuova Tecnodelta Production, high quality bearings and tensioners. Our Distribution kits with water pumps are equipped with all other transmission elements subject to wear (rigid components) and fasteners.
We recommend always replacing all the transmission components to ensure the best maintenance.
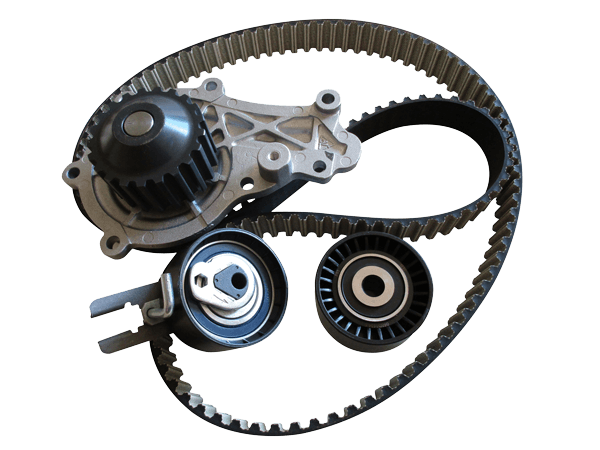
BRAKE HOSES AND CABLES
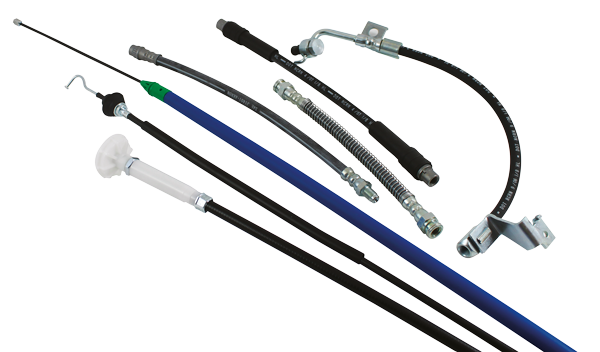